
The SIPOC model allows teams to figure out how S, I, and P are impacting O and C needs.Īctionable insights into factors that are affecting customers create significant improvement opportunities. With in-depth knowledge of the underlying causes of problems, organizations can develop practical strategies to improve processes. It enables process management teams to visualize, comprehend, and communicate effectively. The SIPOC model offers a clear picture of the complete process, and the follow-up steps. How Does the SIPOC Model Help in Process Improvement? Tracing and correcting the variations will lead to seamless process integration, improvements, and optimization.

KPOV variations can have a tremendous impact on manufacturability, performance, reliability, and efficiency. The SIPOC model also helps determine variations in KPOV (Key Process Output Variable), which is a factor that results as an output from a process. The SIPOC model is key to business process improvements.īy graphically representing all elements of a process, it keeps everyone onboard, including new employees, informed about the different stages of a process. When the SIPOC diagram is ready, process management teams should share it with all stakeholders for evaluation, rectification, and process improvements. Text message / email / Telephone to inform the customer Here’s a simple SIPOC model example of a vehicle repair facility: They must be able to identify different elements of the process, including who the suppliers are, the inputs required for process execution, the final output, and the customer. To prepare a SIPOC table, process teams must be capable of mapping the entire operation. Regardless of the mode of application, the key components of the SIPOC model - S - I - P - O - C - remain the same. In the POCIS approach, ‘Process’ and ‘Outputs’ are the first two steps that generate requirements for ‘Customers’, supported by ‘Inputs’ and ‘Suppliers’. The manufacturing industry also implements the SIPOC model, but most organizations apply the P - O - C - I - S method. This is because in the service sector, for example, restaurants, customers place their requirements first, and then they get the output (food), which gets facilitated by ‘Process’, ‘Inputs’, and ‘Suppliers’. In the COPIS methodology, ‘Customers’ come first, and then, ‘Outputs’, ‘Process’, ‘Inputs’, and ‘Suppliers’. Key Components of the SIPOC ModelĬompanies in the service industry usually follow the C - O - P - I - S approach. Problems can arise from the supplier’s end they can be associated with input specifications or can be connected to processes and outputs not meeting customer requirements.Ī SIPOC table, or a SIPOC diagram, presents an excellent opportunity for teams, the higher management, and all stakeholders to troubleshoot process-related issues, and accordingly, develop appropriate strategies for improvements. It offers valuable insights into areas where major issues persist. The SIPOC model prompts teams to take into consideration crucial process elements, such as the suppliers of the process, the necessary inputs to the process, the different functions of the process, the expected outputs from the process, and the customer or the end-user, who receives the process outputs.Ī visual tool, SIPOC helps understand the entire process, from its start to the end. Process management teams implement the SIPOC model during the ‘Measure’ stage of Six Sigma DMAIC, to determine relevant factors of process improvements before the work on a project starts. The short for Define, Measure, Analyze, Improve, and Control is DMAIC. The Six Sigma methodology includes various stages, for instance, Define, Measure, Analyze, Improve, and Control. Interested in learning Lean Six Sigma and it’s importance? Check out the Lean Six Sigma Expert Master's Program.

The SIPOC model allows organizations to document their business processes graphically, providing them with a comprehensive view of all key process elements in the form of tables and charts. It is one of the most trusted and oldest techniques to map critical business processes.
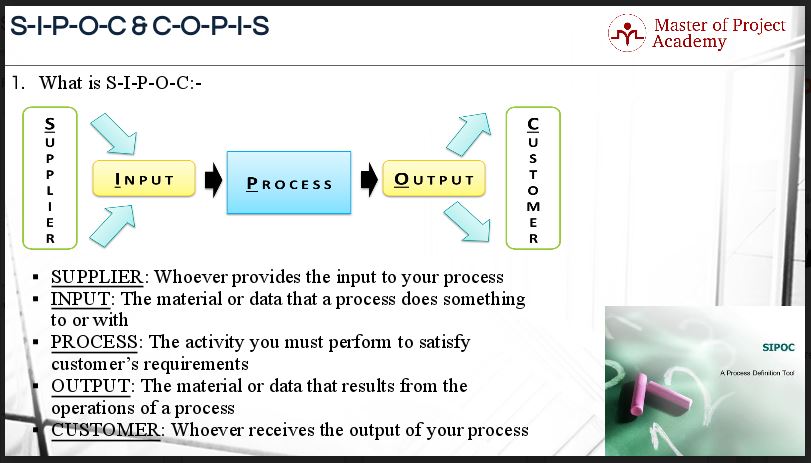
The SIPOC model is a part of the Six Sigma methodology. The innovative Six Sigma method incorporates data-driven, statistics-based tools and techniques designed to facilitate lean manufacturing, better process management, and continuous improvement. Later in 1995, Jack Welch, the then CEO of General Electric, popularized the Six Sigma approach, making it an integral component of GE’s global business strategy. Motorola, Inc., in 1986, developed a unique approach to quality control, and the multinational telecommunications company dubbed it the Six Sigma methodology.
